Most steel products manufactured by the Activar Construction Products Group are finished with a powder-coated paint, providing a more durable coating with a better finish than baked enamel, without the environmental concerns of a solvent paint process.
The Process: steel products are pre-treated to remove oils, metal oxides and welding scales. This pre-treatment both cleans and improves the bonding of the powder to the metal, eliminating the need for a primer. Powder coating is applied as a free-flowing dry powder to steel that is electrostatically charged to hold the powder to the substrate, providing excellent coverage on the inside and outside of corners. After application, the product is exposed to heat in an oven for a specific amount of time, allowing the powder to flow and thermally bond to the substrate, forming a durable hard finish.
Benefits of using powder coat paint technology include:
- Powder coating emits zero or near zero volatile organic compounds (VOC’s).
- Powder coating can produce much thicker coatings than conventional liquid coatings.
- Powder coating overspray can be recycled and allows nearly 100% use of the coating material.
- Paint application is typically very even with no runs or sags.
- Powder coating is thermally bonded to the metal substrate, which provides superior adhesion and prevents chipping.
What about baked enamel?
The Process: steel products are pre-treated to remove oils, metal oxides and welding scales. This pre-treatment both cleans and improves the bonding of the paint to the metal, eliminating the need for a primer in some cases. The coating is paint in a solvent-based suspension which is applied to the steel by spray, brush or roller. After application, the product is exposed to heat in an oven for a specific amount of time, allowing the VOC’s to be eliminated and the paint to cure, and form a durable finish.
How does powder coating compare to baked enamel?
- Enamel wet paint systems use a solvent carrier to convey the paint to the substrate. Elimination of the solvents during the curing process results in high levels of VOC’s and hazardous air pollutants. Powder coating produces no VOC’s.
- When an enamel is applied in a wet form, the surface appearance often shows spray patterns or brush strokes due to the application method, or can pull away from edges as the paint cures. Powder coating produces a smoother finish and better edge coverage.
- Paint thickness can vary and running and sagging are more noticeable. Powder coating has a more uniform application of paint than baked enamel.
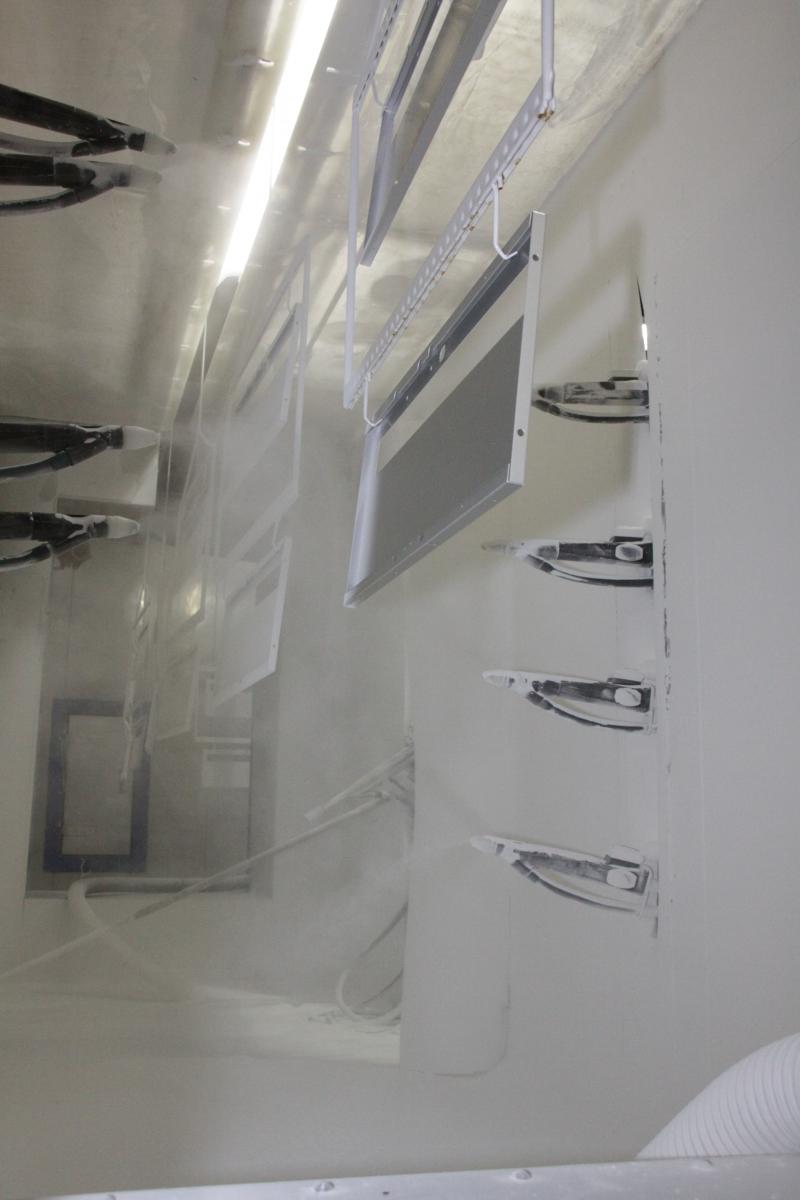